WHAT ARE THE DIFFERENCES BETWEEN PLC AND DCS?
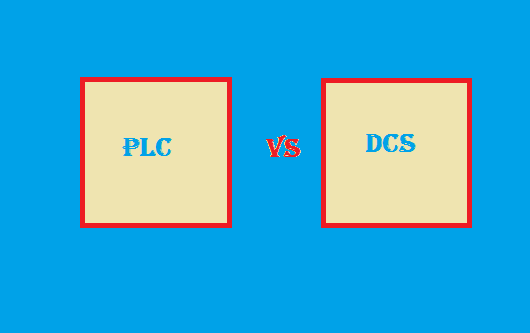
This artical is from : https://automationforum.co/
what is PLC?
PLC is a Programmable Logic Controller is used for automation of electromechanical processes. The PLC is designed for multiple inputs and output arrangements, extended temperature ranges and it have the ability to resist electrical noise and resistance to vibration and impact. Programs to control machine operation are usually stored in battery backed up or persistent storage.
PLC can be described as an electronic system which is operated digitally and designed for use in an industrial environment. It uses a programmable memory for internal storage of user oriented instructions. Those instructions are used for implementing special functions such as logic, sequencing, timing, counting and arithmetic to control, through digital or analog inputs and outputs, various types of machines or processors.
A programmable logic controller is almost same as a small computer with built-in operating system (OS). The OS is highly skilled to handle incoming events at the time of their occurrence. Sensors are connected to the PLC input lines to notify upon events. For example temperature above or below a certain level, liquid level reached etc. and for any reaction to the incoming events it has output lines to signal. For example start an engine, open or close a valve etc. The system is user programmable and it uses a language called ‘Relay Ladder’ or RLL (Relay Ladder Logic) for this purpose.
What is the architecture of PLC?
A PLC is a solid state user programmable control system with the following functions as to control logic, sequencing, timing, arithmetic data manipulation and counting capabilities. PLC can be viewed as an industrial computer that has a central processing unit, memory, input output interface and a programming device.
Every PLC needs:-
• A CPU module
• A power supply module
• At least one I/O module
An integrated PLC contains all of those components in a single unit. Some integrated PLC’s can be expanded by having additional I/O modules PLCs must contain a CPU module, a power supply and I/O modules plugged into the same rack.
What is CPU module in PLC? What are the functions of CPU module in PLC?
The CPU module consists of two main parts as the central processing unit and its memory. The memory includes PROM (Programmable read only memory) containing the PLCs operating system, driver programs and application programs; and also RAM, where the user written programs and working data are stored. PLC manufacturers offer different types of retentive memory to save user programs and data while power is removed, so that the PLC can resume execution of the user-written control program as soon as power is restored. If the PLC has one of the following tentative memory options, it doesn’t have to be reprogrammed each time it is turned on, so a keyboard and monitor not necessary to be included as a part of every PLC.
In most PLCs, at least, part of the RAM memory’s contents is protected by a long-life battery, for years of use. Other PLCs have only capacitor –based power back-up. So RAM memory is saved only for short periods of power outages (measured in hours).Many PLCs also offer removable memory modules, which are plugged into the CPU module. A copy of the user-program and data on EEPROM (electrically erasable programmable read-only memory) chips in the removable memory modules can be possible to the user. An EEPROM module can be connected into any PLC of the same make, so they are also useful in copying programs and data from one PLC to the next.
Now a days, PLC have started to include flash memory, which is like EEPROM memory except that it can be written without the need of special circuitry. Flash memory is used on some removable memory modules as an alternative of using the older EEPROM memory chips, but flash memory is also sometimes built into the CPU module, where it automatically backs up parts of Random access memory even as the PLC runs. And also if the power fails while a PLC with flash memory is running, the PLC will resume running without having lost any important working data after power is restored. Modern CPU modules often contain more than one microprocessor. The main microprocessor chip’s job is to execute the scan cycle while slave microprocessors handle the communication functions required to exchange data with increasingly powerful I/O modules remotely located sensors and actuators, and with other controllers via local area network.
What is DCS?
DCS (Distributed Control System) refers to a control system usually of a manufacturing System, process in which the controller elements are not central in location but are distributed throughout the system with each component sub-system controlled by one or more controllers. It also controls the safety of whole plant operation. This concept increases reliability and reduces installation cost by localising control functions near the process plant with remote monitoring and supervision. DCS was introduced in 1975 by:
Honeywell-TDC 2000
Yokogawa
DCS operates with multiple controllers and it coordinates all job and also it uses conventional control items which are automatically connected.
The comparison between PLC and DCS are as follows:
PLCs are less expensive as compared to DCS system.
Response Time: When comparing the response time of both, the response time of PLCs are 1/10 and which makes it an ideal controller for near real-time actions.While DCS take long time to respond, not a right solution when response time is critical.
Scalability : When compared with DCS system, the scalability of PLC is less. PLC can able to process with a few thousand i/o points while DCS can handle with several thousands i/o points. Hence for an advanced control system spread over a wide area DCS is the best option.
Redundancy: When we need power or fault tolerant I/O, the redundancy of PLC is a problem. DCS is better than PLC in this case. The DCS systems are also in higher level in three programming library, in advanced or optimizing control in self-tuning algorithms and particularly in their total plant architecture and information management capabilities.
Complexity: For complex operations like oil and gas, power plant, chemical plant operation DCS is the suitable one as it requires advanced process control operations and for small scale PLCs are suitable.
Vendor Support: DCS vendors generally requires user to employ them to give integration services and implement process variations. For PLC based systems, the system integrators perform the same function. When the quality of support factor in vendor selection become an important factor, most manufacturers reduced the factory staff and a generation of experienced process control personnel has begun to retire.
Frequent process change: For dedicated processes that does not change often, PLCs are applied. For frequent adjustments and analyse large amount of data in a complex process, DCS is preferred.
Safety :In PLCs, when something is broken, diagnostics will tell you. In DCS, the asset management will informs you to what might break before it does.
PLCs were developed by manufactures that had been making relay for logic and inter-lock applications, while DCS systems were developed by process control manufacturers, having experience in PID-type analog control. Therefore, in the past it made good sense to use each type of controller in its area of superior experiences.
If the I/O was digital, the logical choice is to use a PLC, whereas if the I/O was mostly analog, a DCS system was selected. This logic while still valid to some extent, end- user familiarity has become a decisive factor in system selection.
PLC I/O is likely to be more rugged and PLCs are likely to handle detached logic faster than DCS system.
PLCs are also more desirable. Their language, such as ladder logic are more familiar to plant personnel and therefore these are less, resistance in using them. Ladder logic type languages can be undesirable in some situations because they are not well suited for analog process control
Some users have overcome the limitations of PLCs by integrating them with personal computers using custom-coded programming. The disadvantage to this approach is that such a non-standardised system is generally understood fully only by its designer, and when the person leaves the company, the system can be ruined.
The above mentioned are the differences between PLC and DCS system.